A Personal Perspective on the W12 Series CNC Hydraulic Four Roller Rolling Machine 10X2500
Having worked in metal fabrication for over a decade, I’ve come across my share of machinery that promises more than it delivers. So, when my company decided to invest in the W12 Series CNC Hydraulic Four Roller Rolling Machine 10X2500, I approached the new equipment with both curiosity and a hint of skepticism. However, after several months of consistent use, I can say that the machine has become an invaluable asset to our operations.
Initial Impressions and Setup
The first thing that struck me was the robust and solid build. The machine is undeniably heavy-duty, yet its sleek European design shows that aesthetics weren’t entirely forgotten. The initial setup was relatively straightforward, thanks to comprehensive documentation and responsive technical support from the manufacturer.
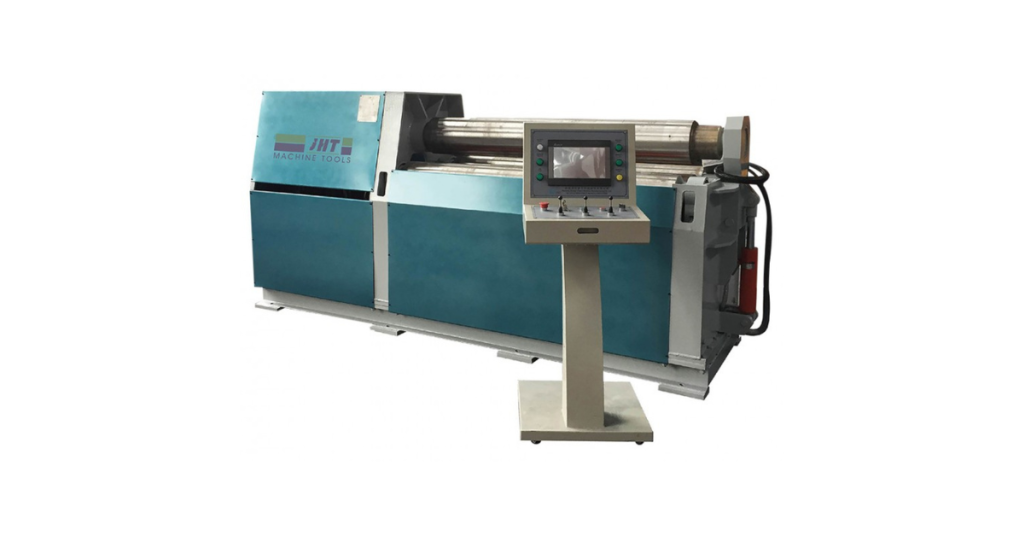
User-Friendly Control System
The PLC touch display CNC control system quickly became my favorite feature. It felt intuitive and responsive, making programming and executing different rolling sequences easy. The pre-programmed settings let me customize rolling parameters based on material thickness, desired shapes, and specific project requirements. Everything at my fingertips streamlined our workflow, drastically reducing the learning curve for new operators.
Control and Programming
The CNC control system offers remarkable flexibility. We began programming straightforward rolling cycles to familiarize ourselves with the interface and gradually explored more complex rolling patterns. One feature that stood out was the system’s ability to simulate a rolling sequence before starting production. This simulation helped us detect potential issues in the setup, reducing the chances of material wastage and allowing us to fine-tune parameters before starting.
When we worked on more intricate shapes like cones, arcs, and spirals, the system didn’t falter. The ability to pre-bend the edges meant we could start each roll with a consistent curve, eliminating flat ends and ensuring tight seams in the final product. Switching between different shapes and angles became almost second nature after programming a few successful runs.
Performance in Action
One clear benefit emerged after working with this machine daily: its ability to deliver consistent results. Rolling cylindrical plates, particularly for storage tanks, had often been a time-consuming task involving a lot of trial and error. But with the pre-bending function, we saw an immediate reduction in flat ends and wasted material.
Switching between different shapes, such as conical and arc, was also remarkably efficient. The four-roller system clamped the plates securely, minimizing the risk of slippage. I noticed this feature most when rolling heavier, thicker plates, which previously posed a challenge due to their weight and rigidity.
Noteworthy Use Cases
One of our major projects involved rolling cylindrical sections for pressure vessels. We had struggled with inconsistencies using previous machinery, but the W12 Series provided precise and consistent results that met stringent quality standards.
In another instance, we were tasked with producing custom cone-shaped structures for a local shipyard. The ease with which we could switch between standard shapes and customized conical forms made the machine worth its weight in gold. The high-grade 42CrMo alloy steel rollers showed minimal signs of wear even after handling these demanding tasks.
Maintenance and Support
After several months of heavy use, I was impressed with how well the machine held up. Routine maintenance checks revealed little wear and tear, and replacing consumable components like seals and lubricants was straightforward. We also received software updates from the manufacturer, which provided incremental improvements to the control system and addressed minor bugs.
The Bosch-Rexroth hydraulic system remained reliable, and the Siemens electrical components continued to function without issues. The robust build quality, especially the 42CrMo alloy steel rollers, ensured the machine could handle even tough materials without significant wear.
Recommendation
The W12 Series CNC Hydraulic Four Roller Rolling Machine 10X2500 combines precision with versatility. Its pre-bending feature, user-friendly controls, and strong build make it suitable for large-scale industrial production and smaller custom jobs.
Purchasing the W12 Series from Beaver Industrial Supply was a positive experience. Their knowledgeable sales team helped us select the right model, and the technical support provided ensured a smooth setup. The seamless buying process and ongoing support reinforced the value of our investment.
Introduction
In the rapidly evolving landscape of metal fabrication, precision machinery is crucial to ensure high-quality and efficient production. The W12 Series CNC Hydraulic Four Roller Rolling Machine 10X2500 stands out as a top-tier choice in this space. This machine offers unrivaled accuracy and ease of operation, enabling manufacturers to roll plates into various shapes with finesse and minimal error.
With a sophisticated European design and a collection of best-in-class components, it’s a go-to solution for a diverse array of industries. This review will explore its design, features, uses, and the exceptional value it provides.
Design & Build Quality
The W12 Series CNC Hydraulic Four Roller Rolling Machine is offered by several leading brands, including JHT1 and PrimaPress, each recognized for delivering reliable, high-quality equipment. Its European design embodies a high level of craftsmanship and precision. Built from welded ST-52 steel, the machine boasts remarkable durability and rigidity, essential for withstanding intense rolling forces over prolonged periods.
The main rolling shafts, materials, and bearings used are of European origin, ensuring that each component is crafted to withstand heavy use while maintaining exacting standards. Additionally, the machine’s main power system relies on Siemens technology, while Schneider supplies electronic components. The hydraulic system from Bosch-Rexroth integrates seamlessly into the machine’s operations, ensuring smooth and reliable performance.
Key Features
- Four Roller System: The machine employs a unique four-roller design. This arrangement enhances bending accuracy by securely clamping the plate between the top and side rollers. It also minimizes the need for additional handling and repositioning.
- CNC Control System: The integrated Programmable Logic Controller (PLC) with a touch display CNC control system provides intuitive and precise control over the rolling process. Operators can quickly adjust settings to meet specific shape and angle requirements.
- Pre-Bending Capability: A significant advantage of this machine is its pre-bending feature. Pre-bending minimizes flat ends and ensures a uniform curve, which is critical for producing perfectly cylindrical or conical shapes.
- Alloy Steel Rollers: The work rollers are made from 42CrMo alloy steel, offering high tensile strength and durability. They handle even the toughest materials without significant wear and tear.
- European-Grade Components: Every key component—from the hydraulic system to the control electronics—is sourced from premium suppliers, ensuring reliability and long-term operational stability.
Applications & Industries
The W12 Series CNC Hydraulic Four Roller Rolling Machine 10X2500 excels at producing high-quality cylindrical, conical, and arc-shaped workpieces. Its precision and adaptability make it ideal for a range of applications, such as:
- Energy Sector: The machine is indispensable for forming large cylindrical tanks and shells used in the storage and transportation of petroleum and gas.
- Transportation Industry: Manufacturers can roll and bend components for various transport vehicles, particularly for train carriages, buses, and heavy machinery.
- Petroleum and Chemical Processing: It creates high-grade piping for petroleum and chemical processing plants.
- Shipbuilding and Marine Engineering: The machine aids in the production of hulls, decks, and other essential marine structures.
- Boilers and Pressure Vessels: Boilers and pressure vessels require precise rolling, and this machine meets their rigorous standards.
- Metal Structures and General Fabrication: The ability to handle a variety of shapes, from arcs to full cylinders, makes it ideal for fabricating structural elements.
Ease of Use & Productivity
Despite its complex engineering, the W12 Series CNC Hydraulic Four Roller Rolling Machine 10X2500 is surprisingly easy to operate. Its user-friendly CNC control panel simplifies the rolling process, making it possible for operators to handle even intricate shapes with ease. Pre-programmed bending cycles save time and improve consistency.
The four-roller system significantly reduces the amount of handling required, which translates to quicker production cycles and fewer interruptions. With pre-bending incorporated, the machine eliminates the need for separate pre-bending equipment, reducing overall production costs and floor space requirements.
Advanced Engineering & Technical Specifications
- Roller Diameter and Speed: The machine is equipped with varying roller diameters to accommodate different materials and thicknesses. The roller speed is adjustable via the PLC control, allowing operators to customize it based on material properties and desired results.
- Plate Thickness Capacity: The machine handles a broad range of plate thicknesses. Its robust hydraulic system exerts significant force, allowing the rollers to bend both thick and thin plates effectively.
- Conic Rolling Capability: The conic rolling function provides a seamless way to create conical shapes, which can be challenging with traditional rolling machines.
- PLC and CNC Precision Control: The PLC and CNC system allows operators to program and automate rolling sequences for consistently high-quality output. The system provides feedback and diagnostics for real-time adjustments.
Innovative Safety Features
- Emergency Stop System: Accessible emergency stop buttons ensure immediate shutdown if any hazard is detected.
- Hydraulic Overload Protection: The hydraulic system includes overload protection to prevent excessive force on the rollers.
- Guard Rails and Fencing: Physical barriers, guard rails, and fencing ensure that workers stay clear of moving rollers during operation.
Maintenance & Longevity
Maintenance is straightforward due to the modular design. Key components like the hydraulic system and electronic control panel are easily accessible. The use of high-quality bearings and steel alloys reduces wear, minimizing frequent replacements.
The software is designed for easy updates, allowing operators to access the latest control algorithms and optimize performance. Comprehensive technical support is available from the brands providing this machine, ensuring users have assistance with troubleshooting and optimizing machine usage.
Conclusion
The W12 Series CNC Hydraulic Four Roller Rolling Machine 10X2500 is a triumph of modern engineering. Its design, features, and technical specifications are meticulously tailored to meet the demands of various industries. Whether the task is rolling thick plates for pressure vessels or creating precision conical shapes for wind turbines, this machine handles it all with efficiency and precision.
Its ease of use, safety features, and low maintenance requirements make it a valuable addition to any metal fabrication workshop. The successful implementation of the W12 Series by numerous companies attests to its reliability and performance, making it a wise investment for any manufacturer seeking to enhance productivity and quality in their operations.